Production of Elbows and Reducers for Underwater Oil & Gas
Posted: 05/23/2024 07:57:54 Hits: 16
Elbows and reducers play a crucial role in the transportation of underwater oil and gas. These components are essential for ensuring the smooth flow of fluids through pipelines, especially in deep-sea environments where pressure and temperature conditions are extreme. Elbows are used to change the direction of the pipeline, allowing it to navigate around obstacles or follow the natural contours of the seabed. Reducers, on the other hand, are used to transition between pipes of different sizes, ensuring a seamless connection that minimizes turbulence and pressure drops. In underwater oil and gas operations, reliability is paramount. Elbows and reducers must be designed to withstand harsh conditions such as corrosion, erosion, and high temperatures. They must also be able to handle rapid changes in pressure without compromising the integrity of the pipeline. Overall, elbows and reducers are indispensable components in underwater oil and gas infrastructure, ensuring efficient and safe transportation of resources from offshore wells to onshore facilities.
Production of elbows and reducers for underwater oil and gas
The production processes of elbows and reducers are similar, both using dedicated molds and hot pressing. Their production processes mainly include re-inspection of welding materials, re-inspection of forged pipe sizes, dedicated mold plus hot pressing, quenching and tempering heat treatment, surfacing welding, non-destructive inspection, dimensional inspection, physical and chemical inspection. Dedicated mold hot pressing and heat treatment processes should be paid more attention to.
1.1 Dedicated mold hot pressing processes
The hot pressing process refers to heating the raw materials (seamless pipes or forged pipes) to a certain temperature and using dedicated molds and tooling to hot press them. This type of process is suitable for producing seamless elbows and reducers, but if there are many specifications, special molds and tooling need to be customized for different specifications. After the forged pipe raw materials pass the re-inspection, they will be cut according to the cutting drawing. Since the product’s stamp information on the end of the forged pipe may be cut off in the cutting process of elbows, the product information needs to be transferred to the forged pipe body to facilitate subsequent traceability. After the blanking is completed, it is heated to the molding temperature; remove it from the furnace and place it in a special hot-pressing mold to ensure that the center of the forged pipe is consistent with that of the mold. After the molding is completed, open the mold and take the elbow, reducer and other products, as shown in Figure 3.
Figure 3 Hot pressing forming of elbows
1.2 Quenching and tempering heat treatment
After forming, elbows, reducers and other products should be subjected to preliminary dimensional inspection. The elbow is inspected by marking on the platform to identify the molding shape of the elbow. Determine the machining line and flush line; in addition, the diameter inspection is carried out using a ball to verify whether the elbow’s ovality, inner diameter and other parameters meet the technical requirements. Preliminarily inspect the inner diameter and outer diameter dimensional data of both ends of the reducer to determine whether preliminary correction is needed and then inspect the length of the reducer; according to the technical drawings and considering the machining allowance of the groove, determine the cutting lines at both ends of the reducer. After the elbow and reducer pass the preliminary inspection, mechanical cutting and quenching and tempering heat treatment are performed. Quenching and tempering heat treatment include quenching and tempering, key parameters such as heating rates, holding temperatures, and holding time should be paid more attention to. After quenching and tempering heat treatment, take an elbow and reducer for mechanical destructive testing.
Production of elbows and reducers for underwater oil and gas
The production processes of elbows and reducers are similar, both using dedicated molds and hot pressing. Their production processes mainly include re-inspection of welding materials, re-inspection of forged pipe sizes, dedicated mold plus hot pressing, quenching and tempering heat treatment, surfacing welding, non-destructive inspection, dimensional inspection, physical and chemical inspection. Dedicated mold hot pressing and heat treatment processes should be paid more attention to.
1.1 Dedicated mold hot pressing processes
The hot pressing process refers to heating the raw materials (seamless pipes or forged pipes) to a certain temperature and using dedicated molds and tooling to hot press them. This type of process is suitable for producing seamless elbows and reducers, but if there are many specifications, special molds and tooling need to be customized for different specifications. After the forged pipe raw materials pass the re-inspection, they will be cut according to the cutting drawing. Since the product’s stamp information on the end of the forged pipe may be cut off in the cutting process of elbows, the product information needs to be transferred to the forged pipe body to facilitate subsequent traceability. After the blanking is completed, it is heated to the molding temperature; remove it from the furnace and place it in a special hot-pressing mold to ensure that the center of the forged pipe is consistent with that of the mold. After the molding is completed, open the mold and take the elbow, reducer and other products, as shown in Figure 3.
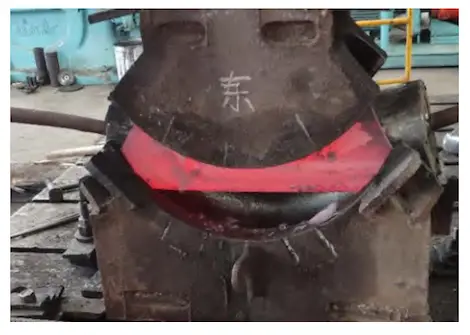
Figure 3 Hot pressing forming of elbows
1.2 Quenching and tempering heat treatment
After forming, elbows, reducers and other products should be subjected to preliminary dimensional inspection. The elbow is inspected by marking on the platform to identify the molding shape of the elbow. Determine the machining line and flush line; in addition, the diameter inspection is carried out using a ball to verify whether the elbow’s ovality, inner diameter and other parameters meet the technical requirements. Preliminarily inspect the inner diameter and outer diameter dimensional data of both ends of the reducer to determine whether preliminary correction is needed and then inspect the length of the reducer; according to the technical drawings and considering the machining allowance of the groove, determine the cutting lines at both ends of the reducer. After the elbow and reducer pass the preliminary inspection, mechanical cutting and quenching and tempering heat treatment are performed. Quenching and tempering heat treatment include quenching and tempering, key parameters such as heating rates, holding temperatures, and holding time should be paid more attention to. After quenching and tempering heat treatment, take an elbow and reducer for mechanical destructive testing.
Post URL: https://www.landeepipefitting.com/production-of-elbows-and-reducers-for-underwater-oil-gas.html
Landee is a professional industrial pipe fitting manufacturer and be well accepted by customers all over the world, we has been producing Pipe Fitting for a variety of applications since 1985. welcome to access our website: https://www.landeepipefitting.com.
Previous: Production of Tees Used for Underwater Oil and Gas
Next: Performance Tests of Tees, Elbows and Reducers
Next: Performance Tests of Tees, Elbows and Reducers